Standard Operating Procedures (SOPs) in the pharmaceutical industry are documents used by an organization to provide step-by-step actions for a specific process. And, according to a published study in ResearchGate, a typical pharmaceutical company must manage an average of 1,250 SOPs with average maintenance taking more than 15,000 hours per company.
Properly-written Standard Operating Procedures (SOPs) in the pharmaceutical industry are essential, as they can reduce mistakes and miscommunication, as well as ensure reliability and consistency across departments.
Creating Standard Operating Procedures (SOPs) in an electronic system provides a new set of challenges and elevates the level of scrutiny by global regulatory entities during health authority inspections to ensure proper and complete compliance with the Code of Federal Regulations (CFR) for Electronic Records and Electronic Signatures (21 CFR Part 11).
To meet regulatory expectations, there are four necessary steps to get companies on the road to compliance once the decision is made to move Standard Operating Procedures (SOPs) in the pharmaceutical industry into an electronic system.
Step 1: Validating the Electronic System
Any electronic system used for generating or housing GxP data, including approved procedures for performing acts related to generating GxP data, should be properly validated.
The level of validation should be based on a justified and documented risk assessment and a determination of the potential of the system to affect product quality and safety and record integrity. The validation process should include a determination of user access, the need for written procedures for use of the system, and a determination of how the system will be managed.
Step 2: Ensuring Data Integrity
All electronic systems used for housing or generating GxP data should go through a data integrity analysis. The system used for Standard Operating Procedures (SOPs) in the pharmaceutical industry should be no exception.
The goal of this analysis is to ensure full compliance with the Principles of Alcoa+ per the FDA and EMA expectations.
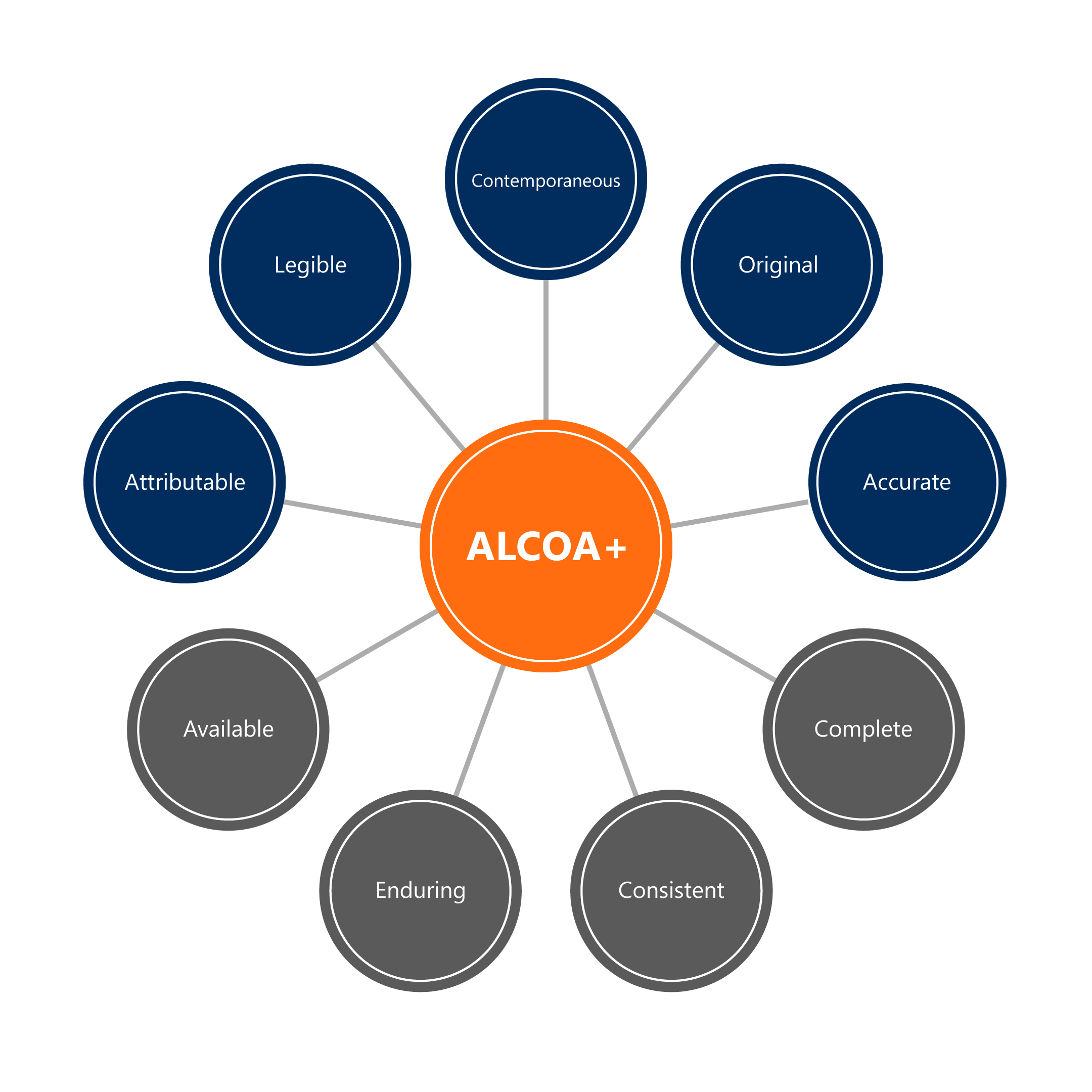
- (A)ttributable-identifiable to the person or system that generated the data
- (L)egible-data can be read and understood
- (C)ontemporaneous-recording data when it occurs
- (O)riginal-original recording of data should be the main record; not copies or transcriptions
- (A)ccurate-a reflection of what happened; error-free
+
- Available-accessible
- Enduring-ensuring data is available long-term
- Consistent-chronological and in an expected sequence
- Complete-nothing has been deleted or lost
Step 3: Enabling Audit Trails
An audit trail is a secure, computer-generated, time-stamped electronic record that allows for reconstruction of the course of events relating to the creation, modification, or deletion of an electronic record.
An audit trail for a document within an electronic document control system, for instance, should include the author of the document, approvers, date and time of any modifications, and a revision history to justify all changes made to the document. Audit trails may need a periodic review, and this review should be determined using risk assessment tools.
Step 4: Performing Periodic Reviews
Two types of review periods should be established for both paper and electronic Standard Operating Procedures (SOPs) in the pharmaceutical industry, as detailed below.
- A review period should be established for determining that content within the Standard Operating Procedures (SOPs) is still current. If content is outdated, the Standard Operating Procedure (SOP) can be revised to update to current processes or regulatory standards.
- A review period should be established as refresher training for those employees that should be responsible for carrying out the procedures within the Standard Operating Procedure (SOP).
Implementation of a new electronic system and migration of current procedures can provide many challenges for an organization within the pharmaceutical industry. This may include the multitude of Standard Operating Procedures (SOPs) that need to be revised, training of current and new employees, or scrutiny from global regulatory agencies during inspections.
Moving forward, experienced and knowledgeable resources are vital to help implement the processes necessary for a successful and smooth transition to an electronic system for Standard Operating Procedures (SOPs) in the pharmaceutical industry.
For questions on migration or further discussion, Please click here to connect with the right resource to respond.
Authored by: Ruth McKnight; Senior Quality and Compliance Specialist, Quality and Compliance.